Read the article
Reading time: 6 minutes
- Fujifilm switched to a more environmentally friendly cleaning technology at its Broadstairs ink manufacturing facility.
- The company partnered with Terrafend, which develops and supplies sustainable cleaning solutions.
- Fujifilm becomes the first company in the world to install an Ambimization® Proteus machine.
- Ambimization® technology provides a revolutionary approach to cleaning by combining chemical and mechanical engineering.
- The water-based cleaning fluids are non-flammable, non-carcinogenic and non-toxic.
- Since installing the new technology, Fujifilm has significantly reduced its waste, carbon footprint and VOC emissions.
The FUJIFILM Specialty Ink Systems (FSIS) award-winning factory in Broadstairs, UK, manufactures high performance inks for a range of markets, including Uvijet wide format UV inkjet inks, and Sericol screen and flexo inks. The factory has implemented several sustainability initiatives over the last ten years and in the summer of 2022, it became the first ever company to trial the new-to-market Ambimization® fluids and Proteus pot wash machine from Terrafend.
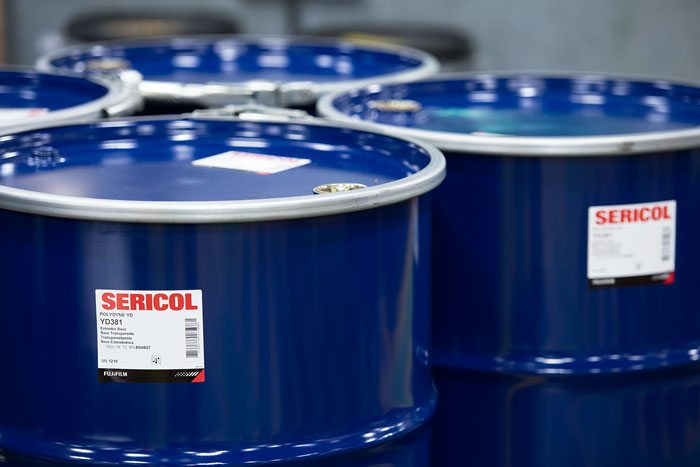
Terrafend’s patented Ambimization® technology combines chemical and mechanical engineering to provide a revolutionary approach to cleaning. Ambimization® water-based fluids are non-flammable, non-carcinogenic and non-toxic. They work at ambient temperatures and can be used repeatedly before reaching end of life, thus reducing workplace risk, energy consumption, and VOCs (Volatile Organic Compounds).
Last year, Fujifilm onboarded Ambimization® technology in its analogue ink department in Broadstairs to clean its UV, water-based and solvent-based ink pots. The use of Ambimization®, in turn enabled Fujifilm to implement the Proteus pot wash machine. These new innovations replaced legacy cleaning equipment that used chemical solvents.
The Proteus machine cleans pots with a water-based Ambimization® fluid in a time-efficient manner, facilitating cost and energy savings, as well as reducing the use of VOCs and creating a safer working environment. It is a sustainable cleaning solution that aligns with Fujifilm’s commitments to promote the use of green technology.
Moving from solvent to water-based cleaning
Fujifilm’s old pot cleaning process involved solvents being sprayed on the walls of the mixing vessels at pressures in excess of 70 bars, thereby removing traces of the ink and decontaminating the surfaces of the pots. This method used around 72,000 litres of chemical-based solvent and generated around 22,000 litres of waste per year.
After the cleaning process, the used solvent, saturated with ink, was pumped into a 24,000 litre storage tank at the Broadstairs site. When full, the tank was drained by a specialist contractor and the solvent waste was removed from the site, via road tanker, to a chemical re-processor. At the re-processor, the waste was separated through distillation, enabling 75% of the solvent to be returned to Fujifilm and used again. A limitation of this method was its inefficiency, with 25% of the material being lost in the recycling process.
In stark contrast, the new Proteus machine and water-based fluids, generate minimal chemical waste and VOCs. With Ambimization®, Fujifilm has managed to reduce solvent waste output at its Broadstairs site. This is not only better for the environment, but safer and more pleasant for the on-site Fujifilm team who handle the ink pots before and after cleaning. Fujifilm has reduced its VOC emissions by 91% since switching to the Proteus and Ambimization® process.
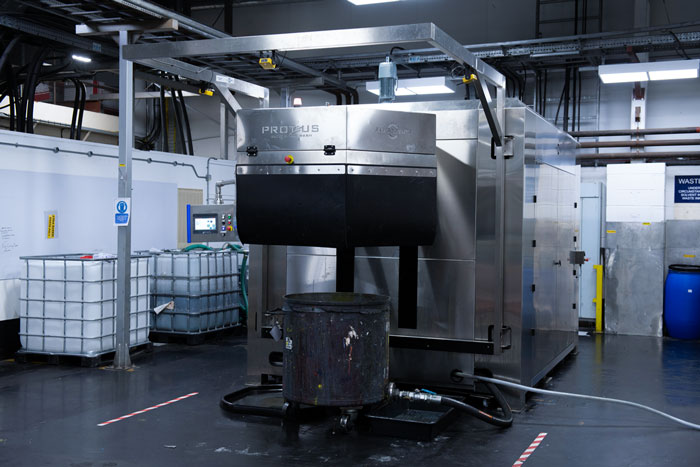
Reduced fire risks & energy consumption
An additional safety benefit of Ambimization® is that it eliminates fire risk – and this is further facilitated by the Proteus machine. With the traditional cleaning method, the solvent formed fine aerosol particles during each cleaning event, because of the high pressure deployed. This created an explosive (ATEX) atmosphere. Although ATEX equipment was installed and steps were taken by staff to reduce this fire risk, the risk still posed a threat.
Moving forward with the more sustainable cleaning solution provided by the Proteus machine, Fujifilm will be able to remove all ATEX rated equipment and save on time that would otherwise have been spent on ATEX health and safety measures within the pot wash area. The Proteus machine is also expected to reduce energy usage by 110,000 kWh per year, making it a hugely worthwhile investment.
Key takeaways
Fujifilm’s ink R&D and manufacturing facility in Broadstairs, Kent, has regularly made the news as a four-time winner of the UK’s Best Process Plant in 2013, 2015, 2016 and 2017, but it is for its sustainability initiatives that it is now rapidly creating waves.
Fujifilm has paved the way for more ink and coating manufacturers to implement Ambimization® by being the first company in the world to pioneer the technology. Since Fujifilm onboarded Ambimization® – and the Proteus pot wash machine – Terrafend has introduced the technology to seven additional international major coating and composite manufacturers.
Switching to Ambimization® has delivered the following objectives:
- Provided a green / sustainable pot cleaning process
- Reduced VOC emissions at the Broadstairs site
- Reduced energy consumption by approximately 110,000 kWh per year during the pot cleaning process
- Future-proofed the Broadstairs site’s pot cleaning capability
- Eliminated the Broadstairs site’s DSEAR risk
Gary Burgess, Manufacturing and CI Manager at FUJIFILM Speciality Ink Systems, comments: “We’re thrilled to be the first company in the world to have trialled an Ambimization® Proteus machine, installed at our Broadstairs ink manufacturing site. Although the digital ink market continues to grow, screen and flexo inks are still used for a number of printing applications. We’ve taken a step to reduce waste and energy when it comes to cleaning our ink pots. During the process, we’ve also reduced VOC emissions and eliminated the site’s largest risk.”
Emily Cassius, Head of Business Development at Terrafend, adds: “This cleaning technology has huge potential to help leading brands – like Fujifilm – to operate more efficiently while reducing risk, waste and carbon footprints. We are pleased to have helped them boost their sustainability credentials and look forward to a continued partnership.”
Learn more about our Label & Packaging solutions
Visit SectorThank you for your enquiry, someone will be in contact soon.