Case study
Eco Flexibles doubles production capacity since investing in two Fujifilm Jet Press FP790 presses
Reading time: 6 minutes
Highlights
Business Growth & Investment: Doubled turnover in 18 months after investing in two Fujifilm Jet Press FP790 presses, becoming the first user outside Japan and winning industry recognition.
Sustainabilty Focus: Strong commitment to eco-friendly packaging using recyclable, compostable solutions and low-impact production methods supported by the FP790.
Technology Impact: The FP790 enabled high quality, efficient digital printing, allowing a shift from flexo and the ability to handle smaller, flexible orders.
Market Expansion: Expanded from food into wellness sectors like supplements, with plans to introduce new substrates and more paper-based packaging.
Future Plans: Potential of a third press and targeting international growth, particularly in the North American market.
“The print quality is exceptional and the consistency is spot on.”
Simon Buswell, Director | Eco Flexibles
Eco Flexibles, a UK-based flexible packaging business, has doubled its turnover in just 18 months following its investment in two Fujifilm Jet Press FP790 presses, as demand for sustainable flexible packaging has soared. Known for its strong focus on sustainable packaging solutions across the food and wellness sectors, the introduction of two Jet Press FP790 presses, has allowed the company to capitalise on market trends and grow the business rapidly.
The first Jet Press FP790 press was installed in June 2023 and the results were immediate. Following the success of the first machine, Eco Flexibles installed a second press later that year to keep up with soaring demand.
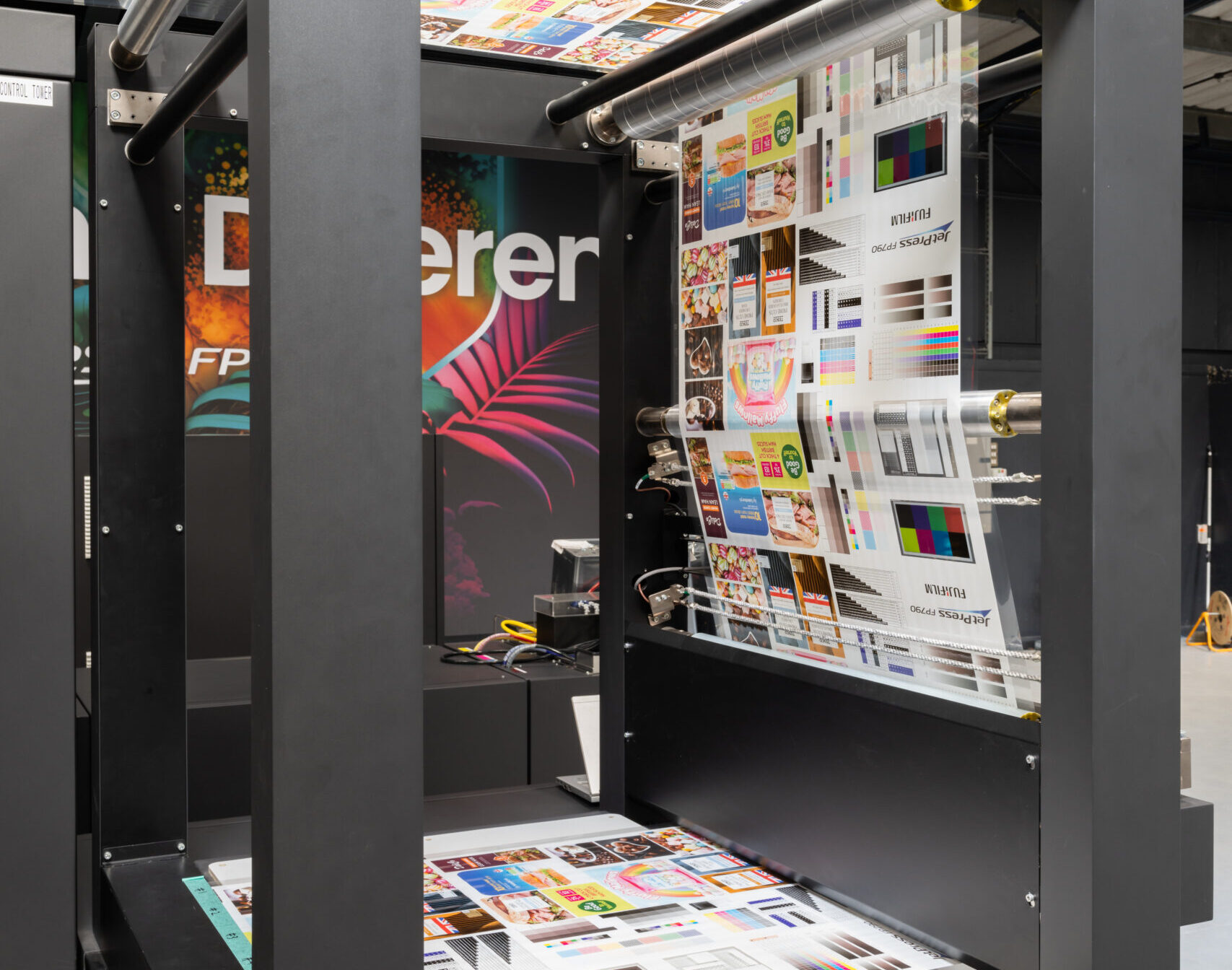
Eco Flexibles has already been recognised for its growth, winning an industry award with The Grocer, for Flexible Plastic Pack of the Year.
Eco Flexibles made headlines back in 2023 as the first customer outside of Japan to invest in the Jet Press FP790. Simon Buswell, Director at Eco Flexibles, comments: “That was a huge moment for us. We knew we were taking a leap into something that hadn’t been widely proven outside of Japan, but we had complete confidence in Fujifilm and the technology. We were willing to lead the way, and it’s paid off.”
Eco Flexibles made headlines back in 2023 as the first customer outside of Japan to invest in the Jet Press FP790. Simon Buswell, Director at Eco Flexibles, comments: “That was a huge moment for us. We knew we were taking a leap into something that hadn’t been widely proven outside of Japan, but we had complete confidence in Fujifilm and the technology. We were willing to lead the way, and it’s paid off.”
Sustainability is central to everything the company does. Buswell continues: “We’ve always focused heavily on sustainability – whether it’s through using mono-materials, recyclable pouches, compostable solutions, or solvent-free, water-wash plates. Our business is built around environmentally conscious packaging. Prior to investing in the Jet Press FP790, we had already been working closely with Fujifilm through our use of the company’s Flenex FW water-wash flexo plates, and the move to digital was the next logical step in our sustainability journey.
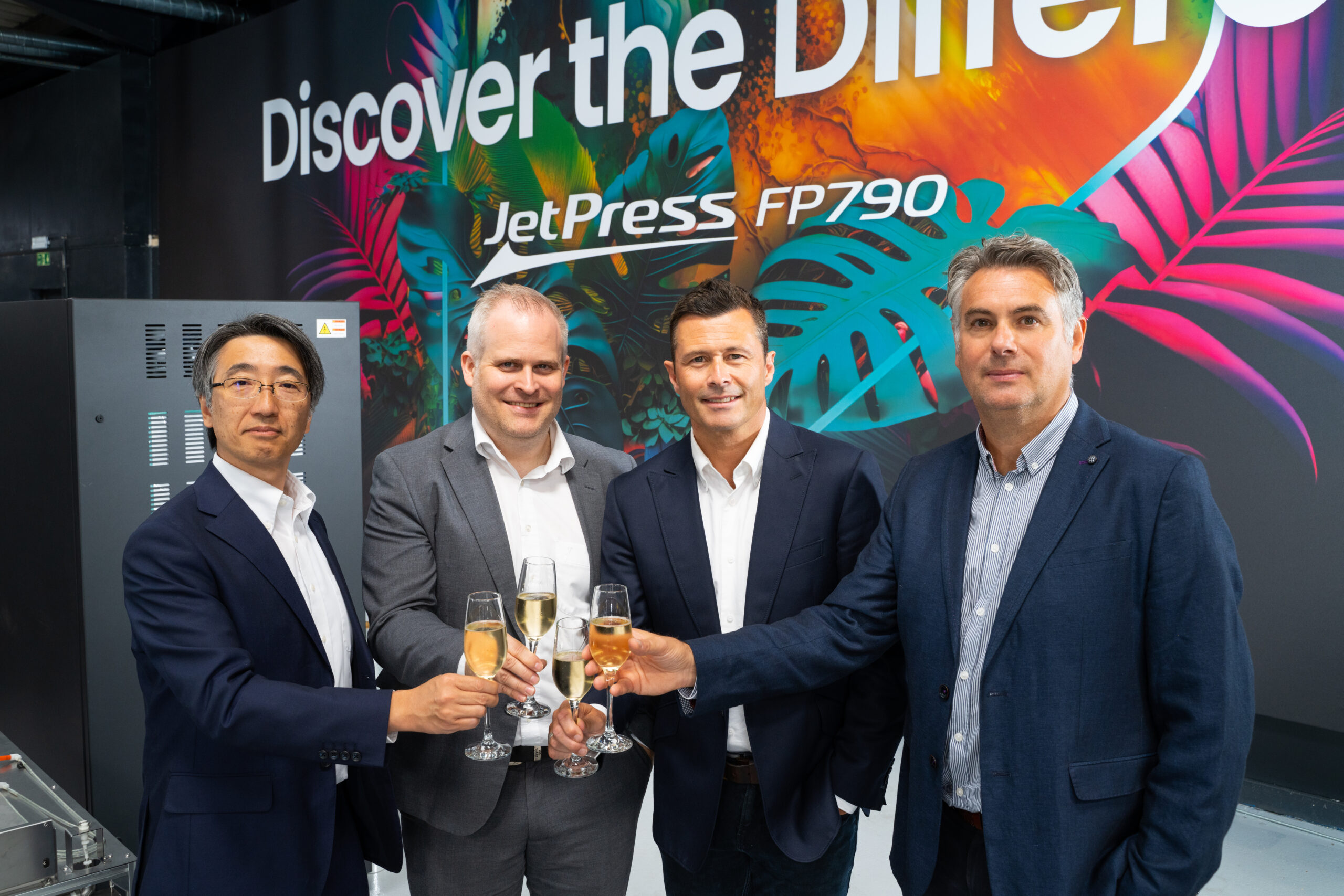
“The FP790 fitted right into our business model – no solvents, minimal waste, low energy consumption, and high print quality. It has allowed us to meet all of our environmental targets. We did a lot of testing and trials, and it became clear that this press represented the future of flexible packaging.
“We originally expected to compete against other digital platforms, but we’ve actually been eating into the flexo market instead. The speed, quality, and commercial viability of the press means we’re now able to take on more work and handle smaller order volumes for our customers, which has been a game-changer.
“We invested in a second machine, due to a mix of necessity and planning. We were using up most of the capacity of the first machine within months. The second gave us the ability to scale while also providing valuable contingency. We’ve doubled our turnover over the last 18 months, and the bulk of that growth is thanks to digital.”
The business currently operates a 50/50 mix of digital and flexo, but Buswell anticipates that digital will continue to grow as they convert more traditional work over to their newer systems.
Customer feedback has been overwhelmingly positive, even from clients who may not fully understand the technical advantages of the Jet Press FP790. “Most of our clients aren’t aware that it’s digital – they just see the results. But once they know, it becomes a real selling point. The print quality is exceptional, and the consistency is spot on.”
Eco Flexibles is also now seeing increasing interest from outside their traditional food packaging markets, particularly in the growing wellness and supplements sector. “We’ve picked up brand new work in new markets – such as health and wellness packaging – things like collagen powders and mushroom blends. It’s a growing market, and like food, it comes with strict regulatory and quality demands, which the Jet Press FP790 helps us meet effortlessly. We are also looking at expanding into new substrates and applications.
“There’s a lot of opportunity to introduce more paper-based packaging into our portfolio. That’s a big focus going forward. We’re also planning to grow internationally, with North America a likely next step.”
Commenting on whether they would consider adding a third Jet Press FP790, Buswell remains open: “Never say never. The demand is there, and we know Fujifilm offers the right technology to meet it.”
“Fujifilm have been fantastic. From the early conversations to installation and support, they’ve really understood what we’re trying to do as a business. We’re not just looking for faster print – we want smarter, greener, more future-focused packaging. The Jet Press FP790 gives us that, and more.”
Manuel Schrutt, Business Strategy Packaging Director, Global, FUJIFILM Corporation comments: “We’re incredibly proud to see the growth that Eco Flexibles has seen since partnering with Fujifilm. As the first customer outside of Japan to invest in this technology, they’ve truly led from the front – proving not just what the press can do, but what’s possible for the future of sustainable flexible packaging. Their success is a testament both to their vision and ambition, and to the capability of the Jet Press FP790.”