Case study
LOGO-Werbetechnik GmbH enhances print quality and uptime with Fujifilm’s Acuity Ultra R2
Reading time: 5 minutes
Highlights
Investment in Advanced Technology: LOGO-Werbetechnik GmbH in Alsdorf, Germany, invested in the Fujifilm Acuity Ultra R2 to enhance print quality, improve production efficiency, and meet growing customer demands.
Need for Equipment Upgrade: The company recognised its older 5-metre machines were no longer sufficient to meet the increasing needs of its clients, prompting the search for a more advanced printing solution.
Improved Production Capabilities: Since the September 2023 installation, the Acuity Ultra R2 has significantly improved print quality and speed, enabling LOGO-Werbetechnik GmbH to produce 5-metre-wide prints, attracting new business and increasing orders.
Partnership with Fujifilm: The successful integration of the Acuity Ultra R2 was supported by a strong partnership with Fujifilm, including comprehensive training and responsive technical support.
Market Expansion and Future Growth: With the Acuity Ultra R2 now fully operational, LOGO-Werbetechnik GmbH is positioned for further market expansion, offering a broader range of services and continuing its commitment to delivering high-quality results.
The Acuity Ultra R2 is a game changer for us, particularly in an industry where flexibility and reliability are key.
Caroline Bertram, Managing Director | LOGO-Werbetechnik GmbH
LOGO-Werbetechnik GmbH, a leading provider of innovative printing solutions based in Alsdorf, Germany, has recently invested in the Fujifilm Acuity Ultra R2 – a state-of-the-art large-format printer. This strategic acquisition is part of LOGO-Werbetechnik GmbH’s ongoing commitment to enhancing its print quality, improving production efficiency, and exceeding the expectations of its customers.
In an ever-evolving industry where speed, quality, and flexibility are paramount, LOGO-Werbetechnik GmbH recognised the need to upgrade its printing capabilities. The company’s previous 5 metre machines were no longer meeting the demands of its growing clientele, prompting a search for a more advanced solution. In December 2022, LOGO-Werbetechnik GmbH first became aware of the Acuity Ultra R2 through a recommendation from Ulrich Frohn, part of the Fujifilm organisation.
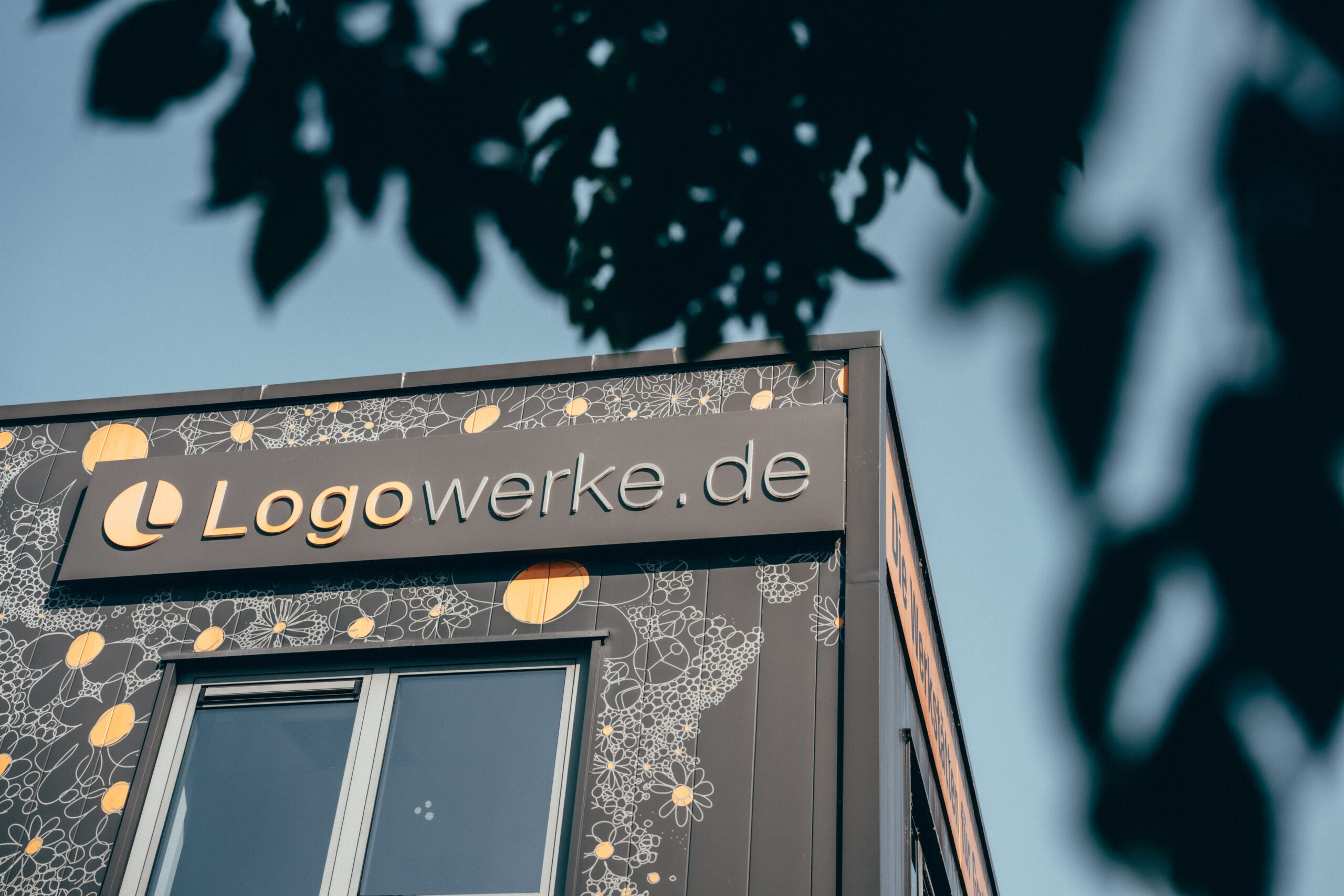
“We were impressed by the Acuity Ultra R2’s remarkable features from the outset,” says Caroline Bertram, Managing Director at Logo GmbH. “Its intuitive operation and the sheer quality of output it promised gave us confidence that this was the right investment for our business. The installation of the printer in September 2023 marked the beginning of a new chapter for our production line.”
Since the installation of the Acuity Ultra R2, LOGO-Werbetechnik GmbH has seen a significant improvement in both the quality and speed of its large format prints. The new printer has enabled the company to produce prints at a width of 5 metres – something that was previously unattainable with its older equipment. This has not only satisfied existing customers, it has also attracted new business too.
“Our clients are thrilled with the results,” Bertram adds. “The feedback has been positive, with many noting the noticeable increase in quality. This improvement has directly contributed to an upturn in orders, reaffirming our decision to invest in this technology.”
The printing industry faces continuous pressure to deliver high quality results quickly and efficiently. The partnership with Fujifilm, and specifically the proven benefits of the Acuity Ultra R2, have been crucial in helping LOGO-Werbetechnik GmbH to navigate these challenges.
Bertram continues: “The Acuity Ultra R2 has transformed our production process. The machine’s speed and precision allow us to meet even the most demanding deadlines without compromising on quality. The printer is a game changer for us, particularly in an industry where flexibility and reliability are key.”
The successful integration of the Acuity Ultra R2 into LOGO-Werbetechnik GmbH’s operation is also a testament to the strong partnership with Fujifilm. The installation process was smooth, and the training provided by Fujifilm at its Broadstairs UK, facility was comprehensive.
“We’re very pleased with the support we received from Fujifilm,” says Bertram. “Their technicians have been responsive and knowledgeable, ensuring that any issues are quickly resolved. The training was also invaluable, equipping our team with the skills needed to maximise the printer’s potential.”
With the Acuity Ultra R2 now fully operational, LOGO-Werbetechnik GmbH is poised to further expand its market presence. The company anticipates that the enhanced production capabilities will open doors to new opportunities, allowing them to cater to a broader range of clients and applications.
“The Acuity Ultra R2 has already proven to be an excellent investment,” Bertram concludes. “Its ability to deliver consistent, high quality results aligns perfectly with our commitment to excellence. We’re excited about the future and confident that this technology will continue to support our growth.”
Ali Meybodi, Sales Manager Wide Format, Fujifilm Germany comments: “We are delighted that LOGO-Werbetechnik GmbH has chosen the Acuity Ultra R2 to enhance its printing capabilities. Our aim is to provide our customers with the tools they need to succeed in a competitive market, and we are proud to support LOGO-Werbetechnik GmbH in achieving their goals.”